Old VWs never die, (they turn into parts)
It was Sunday and we had nothing to race. We needed parts. There was only one thing left to do. We had to make a trip to Hammond.
In Hammond lives Gary Scurlock, our supplier of esoteric Bug parts and acknowledged guru of all things Volkswagen. If it fits on a bug, Gary has at least one copy sitting in his back yard, or failing that, he knows where one is. Handy fellow to know.
Besides, he was holding for me, a transaxle I had purchased a few weeks ago to have for spare parts. Like crown nuts and backing plates.
On top of that he was in the process of restoring an old formula vee to use in the Vintage races and we wanted to take a look at it.
When we arrived, Gary was already in his shop working on the vintage car. He stopped work long enough to chat with us and show off what he was working on.
It is an old Autodynamics, a design that came initially from Ray Caldwell if my memory serves. Ray would go on later to design the famous D-13 and D-13S series, the first vees ever subjected to the MIT wind tunnel. Now he designs chassis for NASCAR.
Gary is doing a beautiful job on the bodywork of the Vee, using techniques more often seen in fiberglass boat building than automobiles. You can track his progress on one of his three web sites.
Naturally he had just the parts we needed. Just on the off chance (I really knew he would have them) I asked about the head shrouds that Mike and Barry were going to require to solve cooling problems. Sure enough he had both the single port for Mike and the dual port for Barry. They were rusty but that is not at all unusual for old VW parts. Some sanding and paint would cure that.
There was some general discussion about the torqueing of the crown nuts on the rear axles. It sounds simple but it is a real problem.
Almost everything else on a bug tends to be a little loosy goosy. Not the crown nuts. They have to be torqued down to somewhere between two hundred seventy and three hundred foot-pounds. That’s a lot. Normally it is achieved by using a three-foot long pipe for leverage on the end of a thirty six-millimetre socket wrench. It is a straining experience and you run the risk of either a stripped thread or a hernia. Not fun. When that happens, you start looking for a new axle…..or a truss.
Of course Gary had a magical mystery tool to do the job. It bolts directly to the brake drum and through the use of gears, multiplies the torque by ten. No more straining on a long handle. Beautiful. Thirty pounds on the torque wrench equals three hundred pounds on the crown nut.
With the transaxle and shrouds in the truck and the borrowed magic tool under our arm, we let Gary get back to his work, and headed home.
It was almost time for the Saints game.
In Hammond lives Gary Scurlock, our supplier of esoteric Bug parts and acknowledged guru of all things Volkswagen. If it fits on a bug, Gary has at least one copy sitting in his back yard, or failing that, he knows where one is. Handy fellow to know.
Besides, he was holding for me, a transaxle I had purchased a few weeks ago to have for spare parts. Like crown nuts and backing plates.
On top of that he was in the process of restoring an old formula vee to use in the Vintage races and we wanted to take a look at it.
When we arrived, Gary was already in his shop working on the vintage car. He stopped work long enough to chat with us and show off what he was working on.
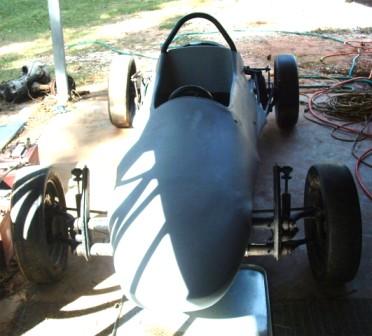
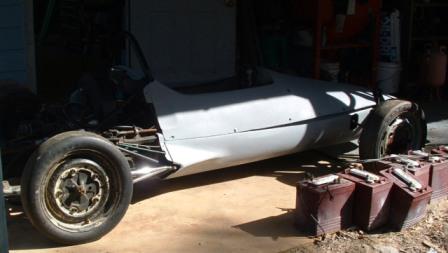
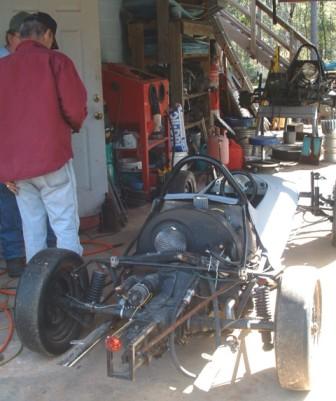
There was some general discussion about the torqueing of the crown nuts on the rear axles. It sounds simple but it is a real problem.
Almost everything else on a bug tends to be a little loosy goosy. Not the crown nuts. They have to be torqued down to somewhere between two hundred seventy and three hundred foot-pounds. That’s a lot. Normally it is achieved by using a three-foot long pipe for leverage on the end of a thirty six-millimetre socket wrench. It is a straining experience and you run the risk of either a stripped thread or a hernia. Not fun. When that happens, you start looking for a new axle…..or a truss.
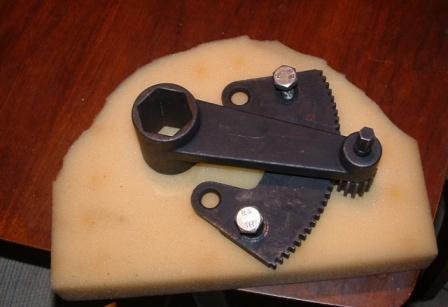
With the transaxle and shrouds in the truck and the borrowed magic tool under our arm, we let Gary get back to his work, and headed home.
It was almost time for the Saints game.
0 Comments:
Post a Comment
<< Home